Introduction
In an era where convenience meets quality, the frozen food industry stands as a beacon of innovation and reliability. The global frozen food market is experiencing robust growth, driven by rising consumer demand for convenient and long-lasting food options. According to a recent report by MarketsandMarkets, the market is projected to reach USD 22.5 billion by 2027, growing at a CAGR of 5.2% from 2022 to 2027.
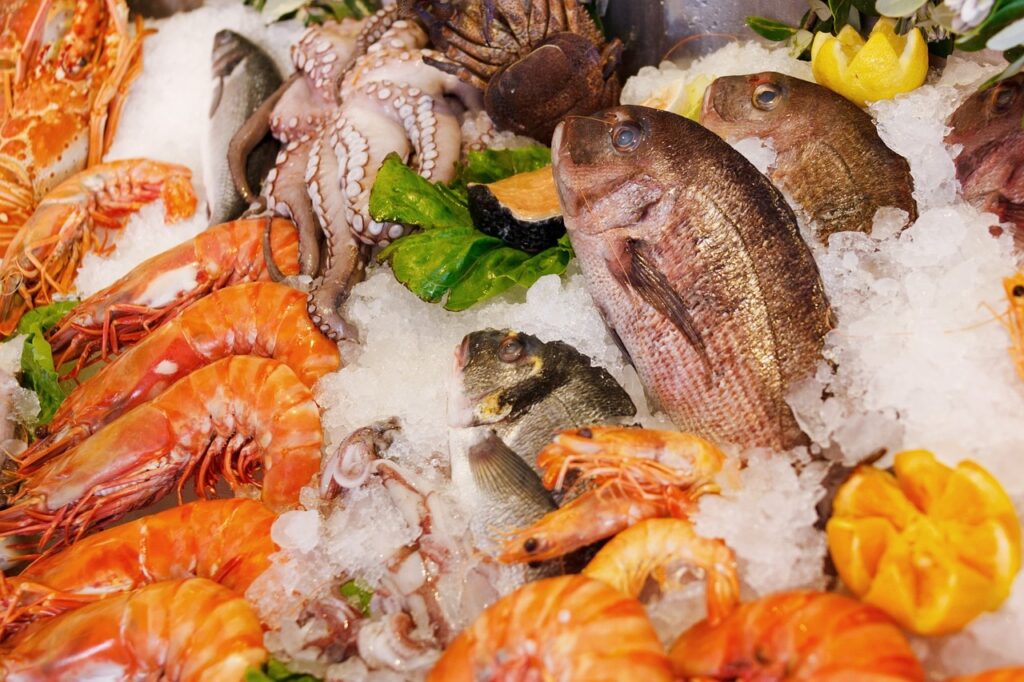
Behind the scenes, frozen food packaging machines are the unsung heroes ensuring that products remain pristine from factory to freezer aisle. These sophisticated machines not only safeguard the freshness and nutritional integrity of frozen foods but also streamline the packaging process, boosting operational efficiency and reducing costs.
Whether you’re a burgeoning entrepreneur or an established manufacturer, understanding the nuances of frozen food packaging machines can propel your business to new heights.
Types of Frozen Food Packaging Machines
Automatic Packaging Machines:Fully automatic systems that manage the entire packaging process with minimal human intervention.
Benefits: High throughput, consistent quality, and reduced labor costs make these machines ideal for large-scale operations.
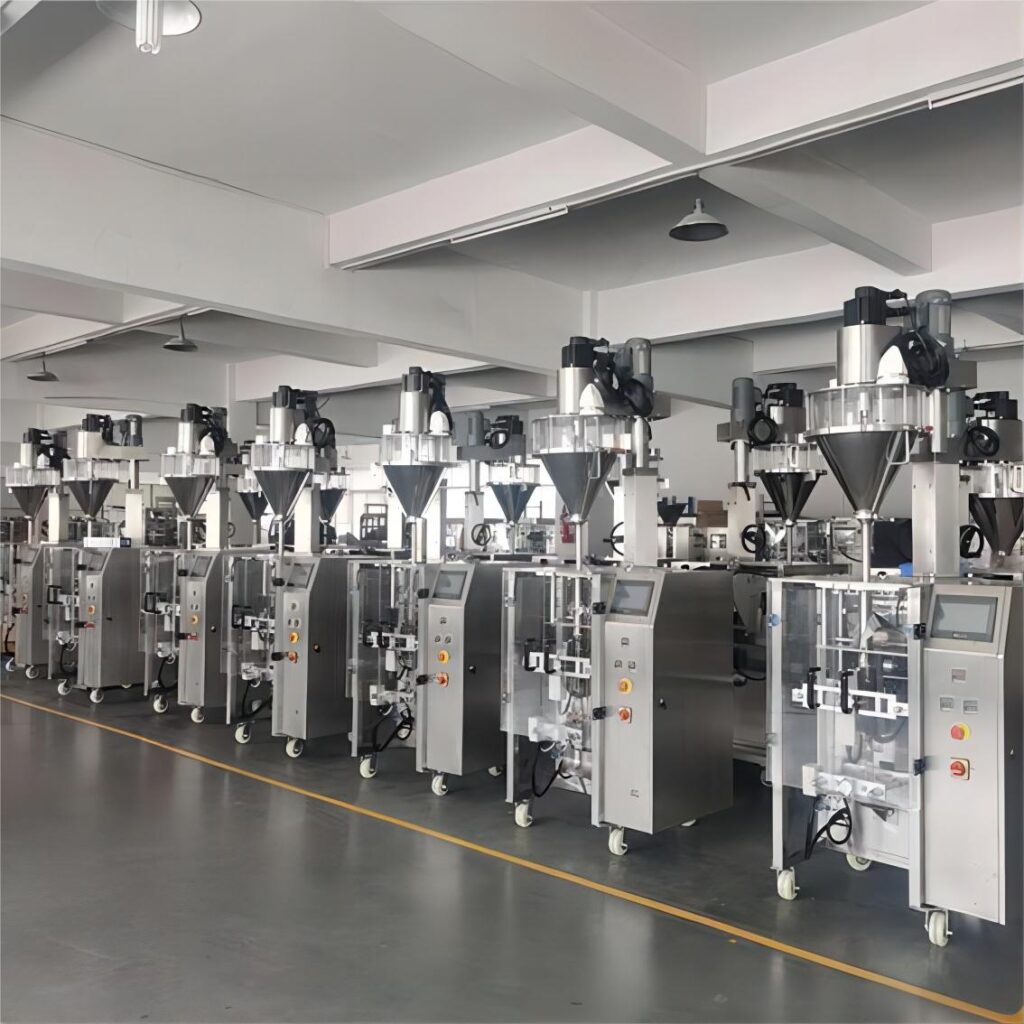
Semi-Automatic Packaging Machines:These machines require some manual input, such as loading products or initiating the packaging cycle.
Benefits: Cost-effective for smaller businesses, offering flexibility and ease of use without the hefty investment of fully automatic systems.
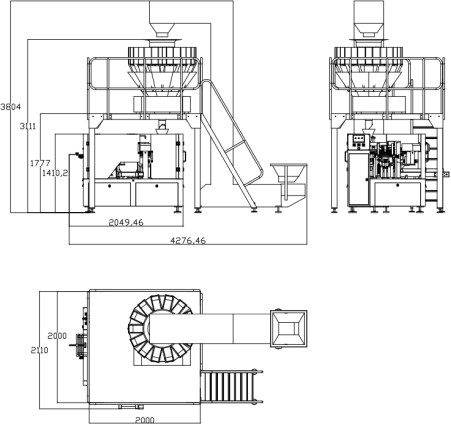
Vacuum Packaging Machines: Specialized machines that remove air from packaging to prevent freezer burn and preserve product freshness.
Benefits: Enhanced shelf life, improved product appearance, and retention of nutritional value.
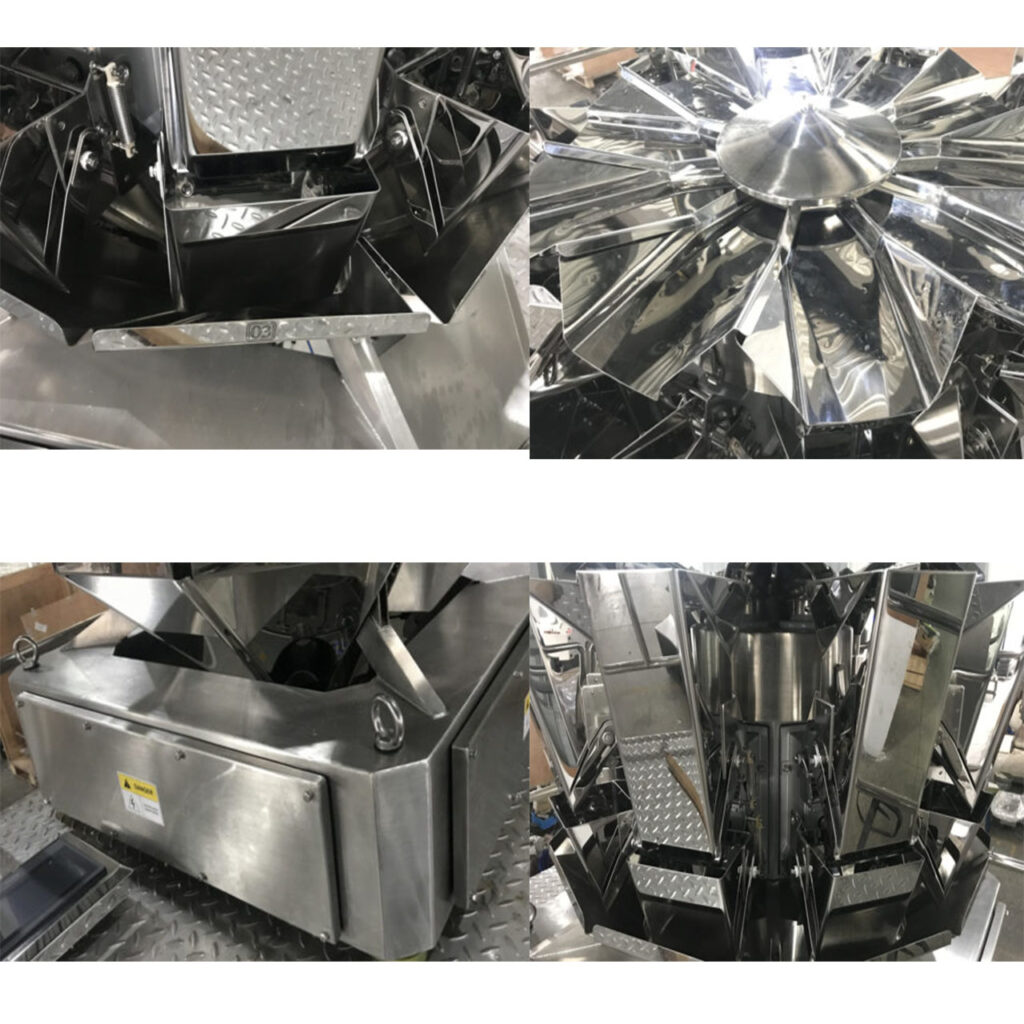
Multi-Head Weighers: Precision instruments that ensure accurate portioning of frozen products before packaging.
Benefits: Minimizes product waste, ensures uniformity, and increases overall production efficiency.
Blast Freezing Packaging Machines: Integrates rapid freezing with packaging to lock in freshness and nutrients.
Benefits: Maintains product quality, minimizes ice crystal formation, and accelerates the packaging process.
Benefits of Advanced Frozen Food Packaging Machines
What will you do when you evaluate machine’s benefit?
Investing in state-of-the-art frozen food packaging machines offers a myriad of advantages that can significantly impact your business’s bottom line and operational prowess.
Enhanced Efficiency and Productivity
Modern packaging machines are designed to handle high volumes with remarkable speed and precision. Automated systems reduce the need for manual labor, allowing you to scale your production without proportionally increasing your workforce. Features like integrated conveyors and automated sealing systems streamline workflows, enabling you to meet rising market demands effortlessly.
Superior Product Quality and Extended Shelf Life
Advanced packaging technologies, such as vacuum sealing and modified atmosphere packaging (MAP), play a crucial role in preserving the taste, texture, and nutritional value of frozen foods. By minimizing exposure to air and moisture, these machines prevent freezer burn and oxidation, ensuring that your products remain fresh and appetizing for extended periods.
Cost Savings and Operational Efficiency
While the initial investment in high-quality packaging machinery may seem substantial, the long-term savings are undeniable. Reduced labor costs, minimized product waste, and lower packaging material expenses contribute to significant cost reductions. Additionally, energy-efficient machines help lower utility bills, further enhancing your profit margins.
Enhanced Food Safety and Compliance
Frozen food packaging machines adhere to stringent hygiene and safety standards, ensuring that your products are free from contamination. Features like stainless steel construction, easy-to-clean surfaces, and automated processes meet regulatory requirements and safeguard consumer health, fostering trust and loyalty among your clientele.
Customization and Flexibility
With a plethora of packaging options available, businesses can tailor their packaging processes to meet specific product requirements. From varying bag sizes and materials to specialized sealing techniques, advanced machines offer the flexibility needed to accommodate a wide range of frozen food products, allowing you to diversify your offerings and cater to different market segments.
Frequently Asked Questions About Frozen Food Packaging Machines
1. How Do Frozen Food Packaging Machines Enhance Operational Efficiency?
Frozen food packaging machines streamline the entire packaging process by automating repetitive tasks, reducing manual labor, and minimizing errors. Features like multi-head weighers ensure precise portioning, while integrated conveyors and sealing systems accelerate the workflow. This automation leads to faster production rates, higher output, and the ability to meet increased demand without additional workforce, ultimately boosting your operational efficiency.
2. What Are the Latest Technological Advancements in Frozen Food Packaging?
The frozen food packaging industry is continually evolving, with several cutting-edge technologies enhancing machine performance:
- Intelligent Control Systems: Advanced PLC (Programmable Logic Controller) systems allow for precise control and monitoring of packaging processes.
- IoT Integration: Internet of Things (IoT) connectivity enables real-time data tracking, predictive maintenance, and remote monitoring.
- Sustainable Packaging Solutions: Eco-friendly materials and energy-efficient machines are gaining popularity to meet environmental standards.
- Smart Sensors: These sensors improve accuracy in weight measurement, sealing quality, and product placement, ensuring consistent packaging standards.
3. What Maintenance Practices Are Essential for Frozen Food Packaging Machines?
Regular maintenance is vital to ensure the longevity and optimal performance of frozen food packaging machines. Key maintenance tasks include:
- Daily Cleaning: Remove any residue or debris from machine surfaces to maintain hygiene.
- Lubrication: Apply lubricants to moving parts to reduce friction and wear.
- Inspection: Regularly check for signs of wear and tear, replacing worn components promptly.
- Calibration: Ensure that weighing systems and sealing mechanisms are accurately calibrated.
- Software Updates: Keep control systems and software up to date to benefit from the latest features and improvements.
4. How Do Frozen Food Packaging Machines Ensure Food Safety?
Frozen food packaging machines incorporate several safety features to maintain food safety standards:
- Hygienic Design: Machines are built with stainless steel and smooth surfaces that are easy to clean and sanitize.
- Automated Processes: Reducing human contact minimizes the risk of contamination.
- Temperature Control: Precise temperature management ensures that food remains frozen throughout the packaging process.
- Regulatory Compliance: Machines adhere to international food safety regulations and standards, such as HACCP and ISO certifications.
Key Considerations When Choosing a Frozen Food Packaging Machine
Choosing and implementing the right frozen food packaging machine is pivotal for businesses to optimize their return on investment, embrace cutting-edge technologies, and seamlessly enhance their production processes, thereby ensuring sustained growth and a competitive edge in the frozen food market.
Production Volume and Scalability
Assess your current and projected production volumes to determine the capacity requirements of the packaging machine. Opt for machines that offer scalability, allowing you to upgrade or expand your packaging capabilities as your business grows. This foresight prevents future bottlenecks and ensures that your investment remains viable in the long term.
Packaging Material Compatibility
Different frozen food products may require specific packaging materials, such as vacuum-sealed bags, rigid containers, or flexible pouches. Ensure that the machine you choose is compatible with the materials you intend to use. Additionally, consider the availability and cost of these materials, as they will impact your overall packaging expenses.
Space and Layout
Evaluate the available space in your production facility to accommodate the packaging machine. Consider the machine’s dimensions, required clearances, and integration with existing equipment to ensure a smooth workflow. Proper space planning enhances operational efficiency and minimizes disruptions during the packaging process.
Budget and Return on Investment (ROI)
Factor in the initial cost of the machine, as well as ongoing expenses such as maintenance, energy consumption, and consumables. Calculate the return on investment (ROI) by comparing these costs against the potential savings and increased productivity the machine offers. A well-chosen packaging machine can pay for itself through enhanced efficiency and reduced operational costs.
Support and Service
Choose a reputable manufacturer that provides comprehensive support, including installation, training, and after-sales service. Reliable customer support ensures minimal downtime and helps address any issues that may arise during operation. Additionally, consider the availability of spare parts and the manufacturer’s response time to service requests.
Success Stories: Businesses Thriving with Advanced Packaging Machines
Case Study 1: Enhancing Productivity with Automation
A mid-sized frozen food manufacturer integrated a fully automatic packaging machine into their production line. The machine’s high-speed capabilities and precise control systems doubled their packaging output while reducing labor costs by 30%. Additionally, the consistent quality of packaging minimized product waste, leading to significant cost savings and increased profitability.
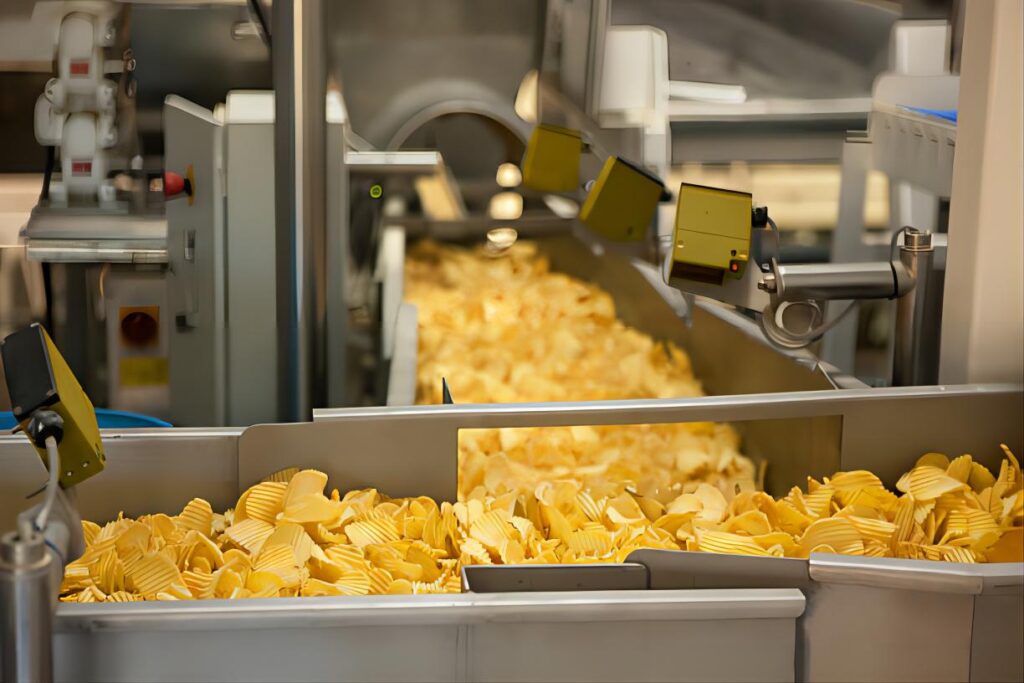
Case Study 2: Improving Product Quality with Vacuum Sealing
A startup specializing in gourmet frozen meals adopted a vacuum packaging machine to ensure the freshness and flavor of their products. The vacuum sealing process effectively eliminated air pockets, preventing freezer burn and preserving the integrity of delicate ingredients. This enhancement in product quality resulted in higher customer satisfaction and repeat business.
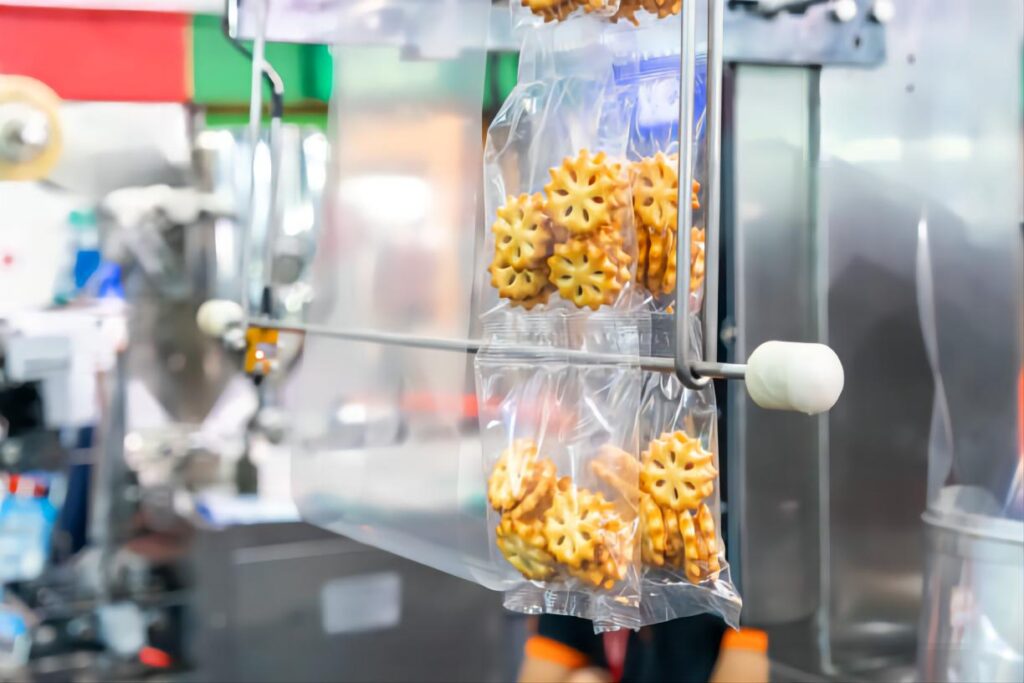
Case Study 3: Scaling Operations with Semi-Automatic Solutions
A family-owned frozen vegetable business transitioned to a semi-automatic packaging machine to accommodate their growing demand. The flexibility of the semi-automatic system allowed them to customize packaging sizes and materials, catering to diverse customer preferences. This adaptability enabled the business to expand its market reach without significant capital investment.
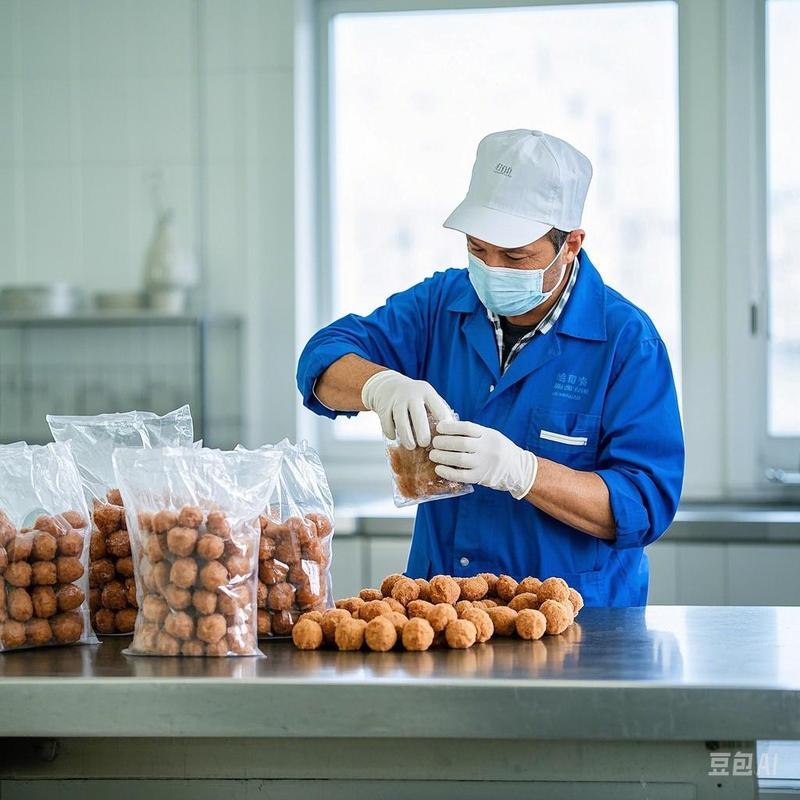
Conclusion
Frozen food packaging machines are engineered to handle the unique challenges posed by frozen products. From maintaining ultra-low temperatures to ensuring airtight seals, these machines incorporate advanced technologies to preserve the quality and extend the shelf life of frozen goods.
Follow BG Machinery ! Embrace the power of modern packaging solutions to elevate your frozen food business, stay competitive in the market, and deliver exceptional value to your customers. Partnering with a reputable manufacturer ensures not only high-quality equipment but also comprehensive support and customization tailored to your unique needs. Step into the future of frozen food packaging and watch your business thrive.