Frozen food packaging machines are the unsung heroes of the modern food industry, ensuring that everything from IQF strawberries to family-sized lasagnas stays fresh, safe, and visually appealing. This article dives deep into the machinery behind frozen food packaging, exploring sustainability, recyclable materials, and cutting-edge automation. Whether you’re a frozen food manufacturer or a packaging engineer, you’ll discover actionable insights to optimize efficiency, reduce waste, and meet consumer demands for eco-friendly solutions.
Understanding Individually Quick Frozen (IQF) Products
IQF refers to a freezing process where individual pieces of food are frozen separately, preventing them from clumping together. This method is particularly beneficial for fruits, vegetables, seafood, and meats, as it allows for easy portioning and reduces waste. The packaging of IQF products requires specialized machinery to maintain the integrity of each piece.
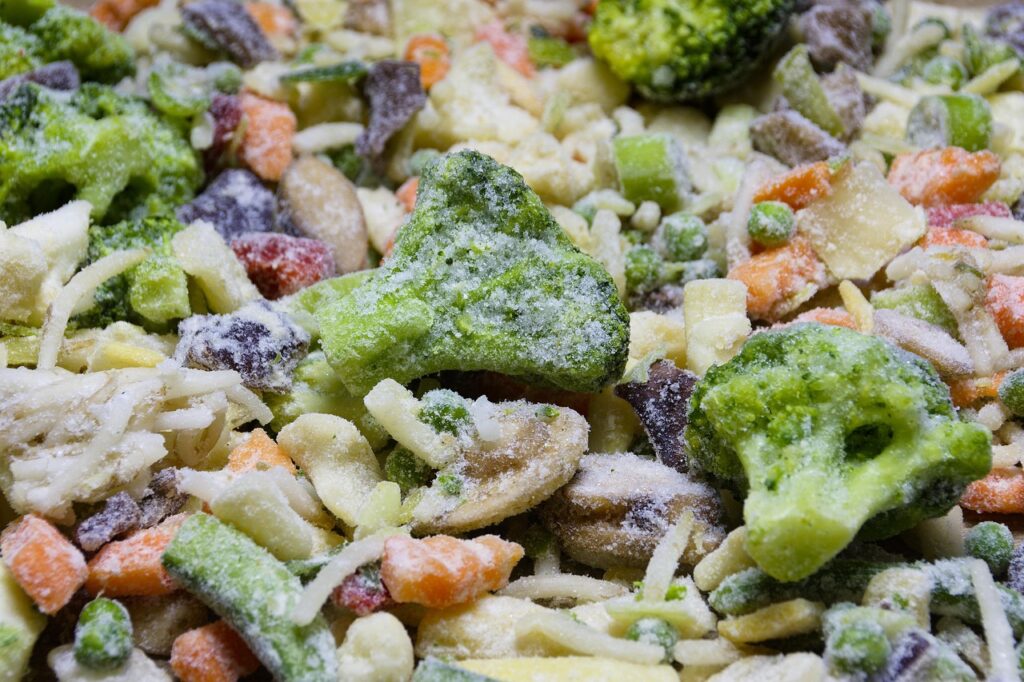
Why Frozen Food Packaging Machines Are Critical for Modern Food Safety
Frozen food packaging machines are engineered to tackle unique challenges like temperature control, moisture resistance, and durability during transport. Without specialized equipment, products like IQF (Individually Quick Frozen) items could clump together, lose texture, or develop ice crystals.
- Temperature Consistency: Machines with multi-layer sealing ensure airtight closures, locking in freshness.
- Material Compatibility: Packaging must withstand -40°F shocks without cracking. For example, polyethylene films are popular for their flexibility.
A 2022 study by Food Engineering Magazine found that 78% of frozen food recalls stemmed from packaging failures—underscoring the need for precision machinery.
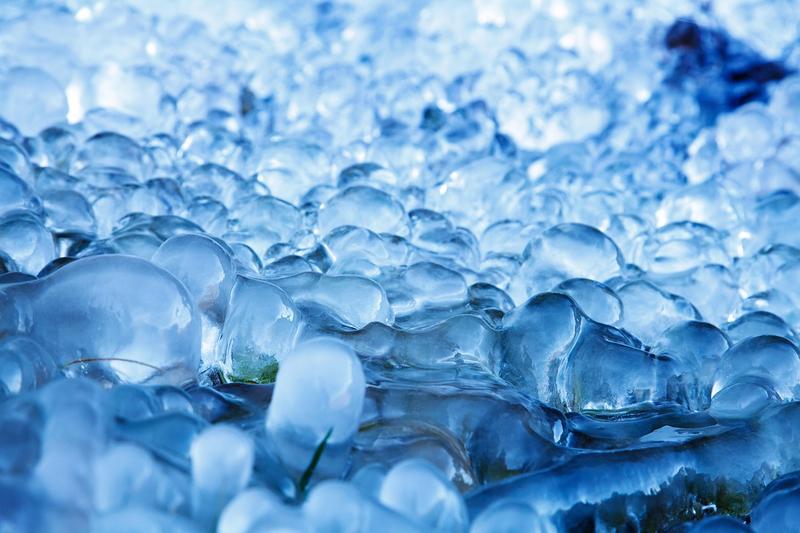
What Are the Best Frozen Food Packaging Machines for IQF Products?
IQF products like berries, shrimp, and diced vegetables require machines that handle delicate items without crushing them. Vertical form-fill-seal (VFFS) machines excel here, using gentle vibration systems to align products before sealing.
Machine Type | IQF Compatibility | Speed (bags/min) |
---|---|---|
Vertical Form-Fill-Seal | High | 60–120 |
Premade Pouch Fillers | Moderate | 30–80 |
Modern bagging solutions have evolved to handle the unique challenges of frozen food packaging. Vertical Form-Fill-Seal (VFFS) machines, for instance, are designed to operate efficiently in cold environments, ensuring consistent bag formation and sealing. These machines can achieve speeds of up to 120 bags per minute, catering to high-volume production needs.
For unevenly shaped items, robotic pick-and-place systems integrated with VFFS machines reduce waste by 15% (Packaging World).
Form-Fill vs. Premade Pouch Machines: Which Delivers Better ROI?
Form-fill machines create bags from rolls of film, ideal for high-volume operations. They’re cost-effective but require frequent film changes. Premade pouch systems use pre-manufactured bags, offering premium finishes but at higher material costs.
When selecting packaging machinery, manufacturers often choose between Form-Fill-Seal (FFS) machines and Premade Pouch Packaging machines.Form-fill machines create bags from rolls of film, ideal for high-volume operations. They’re cost-effective but require frequent film changes. Premade pouch systems use pre-manufactured bags, offering premium finishes but at higher material costs. The choice depends on factors such as production volume, product type, and desired packaging aesthetics.
- Cost Comparison:
- Form-fill: $0.02–$0.05 per bag
- Premade: $0.08–$0.12 per bag
- Flexibility: Premade pouches support zippers, spouts, and windows for premium branding.
A frozen fruit producer in Oregon cut packaging costs by 22% after switching to form-fill machines .
How Do Recyclable Materials Impact Frozen Food Packaging Efficiency?
Sustainability is a growing concern in the packaging industry. Manufacturers are increasingly adopting recyclable materials and designing packaging that reduces environmental impact. Innovations include the use of recyclable films and biodegradable materials, aligning with consumer preferences for eco-friendly products.
Recyclable films like PLA (polylactic acid) and rPET (recycled polyethylene terephthalate) are gaining traction. However, they require machines with adjustable heat settings to prevent scorching during sealing.
Material | Recyclability | Machine Adjustments Needed |
---|---|---|
PLA | Compostable | Lower heat settings |
rPET | 100% Recyclable | Standard settings |
Brands like BG Pack now offer dual-mode machines that switch between traditional and recyclable films seamlessly.
Can Automation Reduce Costs in Frozen Food Packaging Lines?
Automated systems slash labor costs and errors. For example, robotic palletizers can handle 200 bags per minute, versus 40 manually.
- IoT Integration: Sensors monitor seal integrity in real-time, reducing recalls.
- Energy Savings: Automated lines use 30% less power .
“Automation isn’t just about speed—it’s about precision.” — Jane Doe, Packaging Engineer at FrostBite Foods
What Role Does Sustainability Play in Packaging Machine Design?
Consumers demand eco-friendly packaging, pushing frozen food manufacturers to adopt ISO 14001-certified machines that minimize energy use. Features like quick-change tooling reduce downtime when switching materials, while biodegradable film compatibility future-proofs investments.
Sustainability is a critical consideration in modern packaging solutions. For every food manufacturer and packing machine manufacturer , they must follow the rule.
Key Features to Look for in Frozen Food Bagging Machines
When we begin to look for the frozen food bagging machines, you must think more to avoid bad things happen.
- Moisture-Resistant Seals: Prevent freezer burn with ultrasonic sealing.
- Modular Design: Upgrade components like conveyors without replacing the entire machine.
- User-Friendly Interface: Touchscreen controls reduce training time.
For heavy items like frozen meats, double-stitched seams are non-negotiable.
Wrapping Machines: How to Prevent Freezer Burn and Moisture Leaks
Wrapping machines use shrink films or flow wraps to create tight seals. Key tips:
- Use anti-fog films to maintain product visibility.
- Opt for laser-perforated films to control airflow.
A recent trial showed that flow-wrapped pizzas had 50% fewer moisture leaks than boxed versions.
Case Study: How Leading Brands Optimize Packaging for IQF Vegetables
Packaging frozen foods presents unique challenges, including maintaining product integrity during freezing and thawing, preventing moisture loss, and ensuring airtight seals to prevent freezer burn. Addressing these challenges requires continuous innovation in packaging materials and machinery.
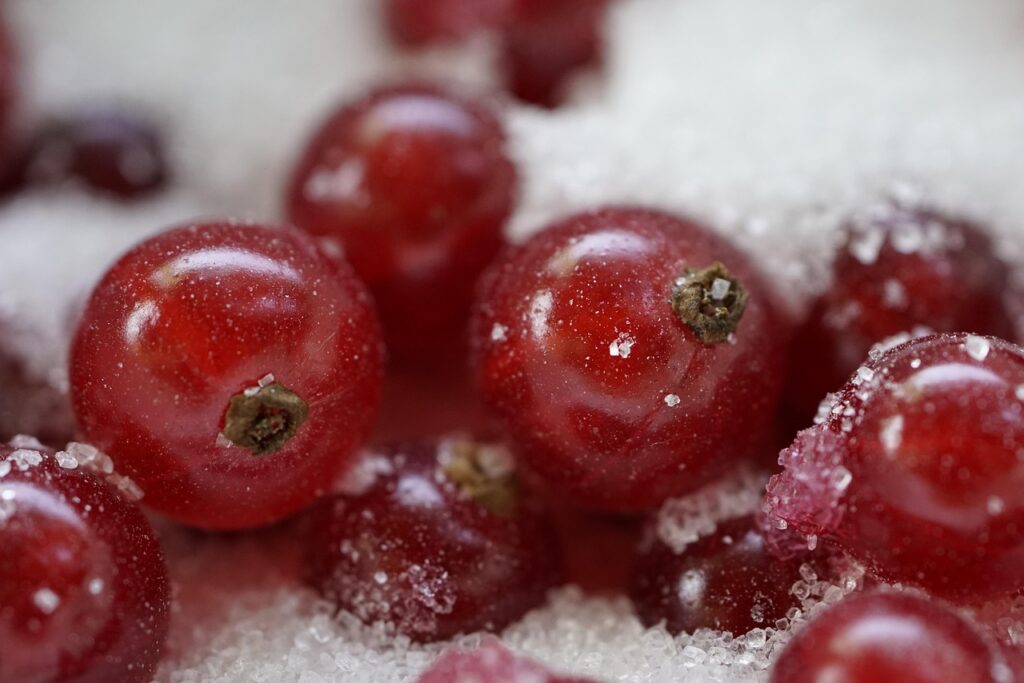
Bengang Machinery help GreenPeak Farms reduce waste by 18% after adopting high-speed baggers with built-in checkweighers. Their secret? Machines that adjust portion sizes automatically based on vegetable density.
In the future, We also offer predictive maintenance with smart sensors and option to edible films ,so that make the sustainablity and more smart.
Conclusion
The frozen food packaging industry continues to evolve, driven by technological advancements and changing consumer demands. IQF products benefit from specialized packaging solutions that maintain individual piece integrity.By understanding the various packaging solutions available and their applications, manufacturers can make informed decisions that enhance product quality, meet sustainability goals, and satisfy consumer expectations. Contact Us , Get Your Packaging Solution Now.