介紹
Automatic cappers have significantly transformed the packaging industry, evolving from simple mechanical devices to highly sophisticated equipment capable of handling a diverse array of bottle sizes and cap types. This comprehensive guide delves into the history, types, and benefits of automatic capping machines, showcasing their crucial role in modern manufacturing processes.
The Origins and Development of Automatic Cappers
Early Innovations and Mechanization
The origins of automatic cappers date back to the early 20th century, coinciding with the rise in demand for mass-produced consumer goods. Initially, capping was a manual task, performed by workers using hand tools. The inefficiency and labour intensity of this process soon highlighted the need for a more efficient solution. This led to the creation of the first automatic cappers, which used basic mechanical systems to increase the speed and consistency of the capping process.
Advancements in Technology
As technology progressed, so did the capabilities of capping machines. One of the pivotal advancements was the integration of pneumatic systems, which utilized compressed air to apply caps with greater force and precision. This innovation allowed for a broader range of bottle sizes and cap types to be handled efficiently, setting the stage for the development of more advanced capping machinery.
Types of Automatic Capping Machines
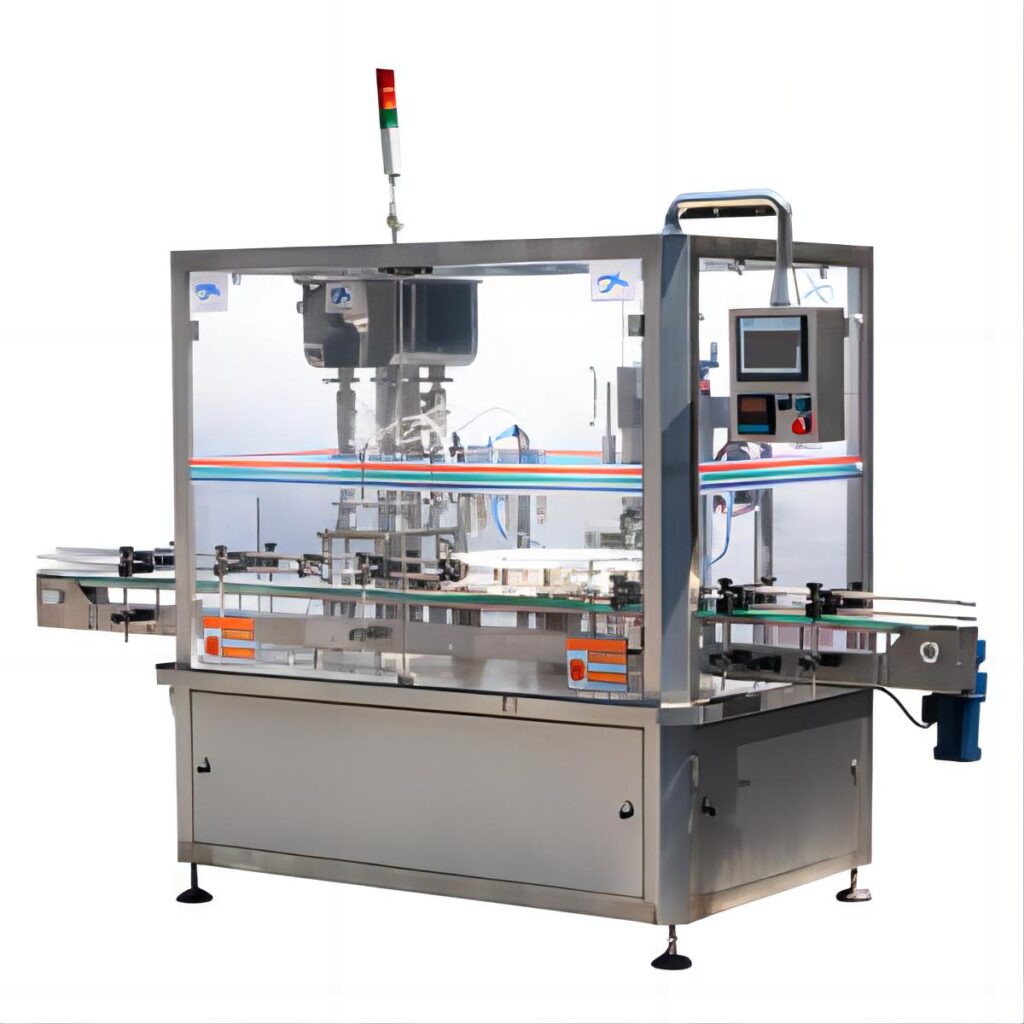
Screw Cap Capping Machine
The screw cap capping machine is designed to apply screw caps to bottles by using a rotating spindle to thread the cap onto the bottle neck. These machines are prevalent in the food and beverage industry, as well as in the packaging of pharmaceuticals and cosmetics. Their ability to ensure tight and secure sealing makes them ideal for products requiring extended shelf life.
Applications and Benefits
- Food and Beverage Industry: Ensures product freshness and prevents leaks.
- 藥品: Provides tamper-evident seals critical for safety.
- 化妝品: Maintains product integrity and prevents contamination.
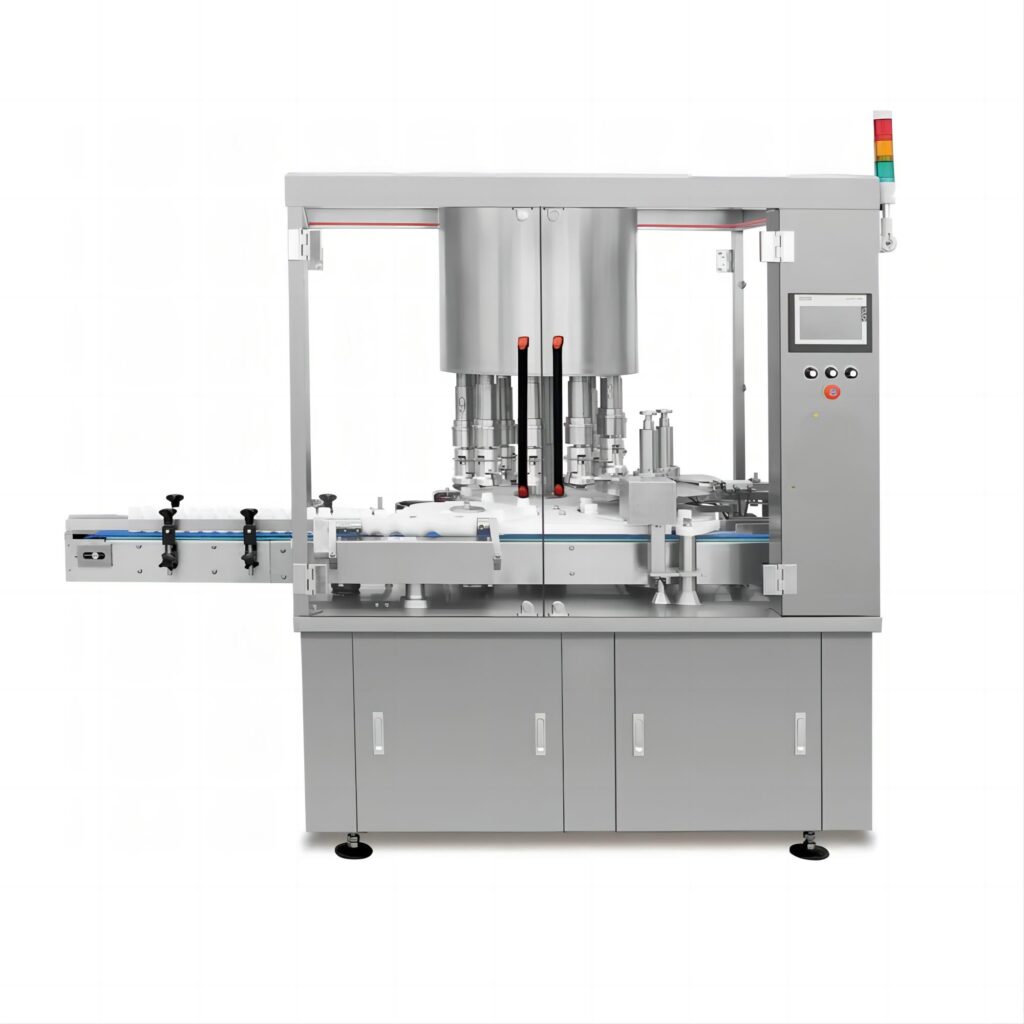
Snap Cap Capping Machine
Snap cap capping machine employ a clamping mechanism to secure caps onto bottlenecks. These machines are particularly suited for smaller bottles, such as those used for condiments, sauces, and personal care products. Their design ensures quick and reliable capping, making them ideal for high-speed production lines.
Applications and Benefits
- Condiments and Sauces: Facilitates easy opening and resealing.
- Personal Care Products: Ensures user convenience and product safety.
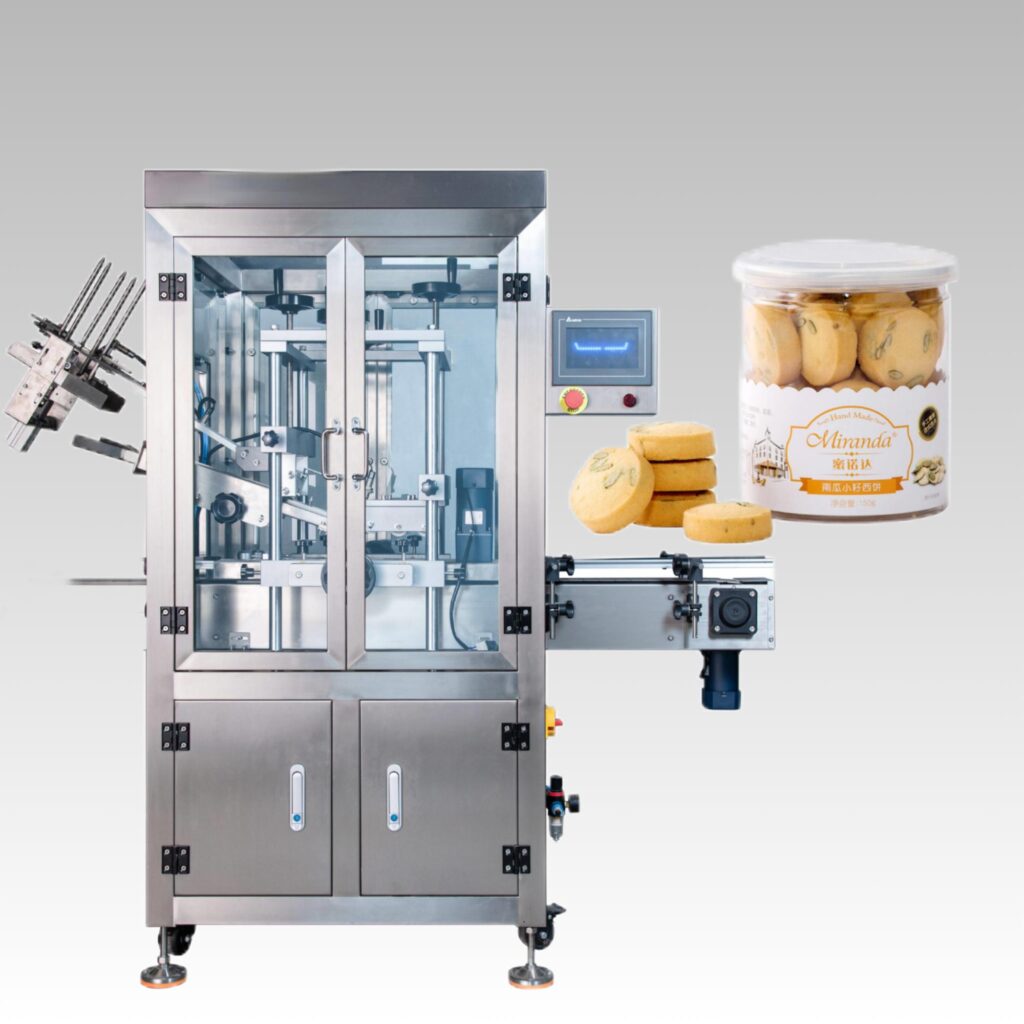
Press-On Cap Capping Machine
Press-on cap capping machines use hydraulic or pneumatic systems to press caps onto bottlenecks. These machines are commonly used for packaging household cleaning products and other non-food items, where a secure seal is essential to prevent spillage and contamination.
Applications and Benefits
- Household Cleaning Products: Prevents leaks and maintains product efficacy.
- Industrial Products: Ensures secure capping for hazardous materials.
Induction Seal Capping Machine
The induction seal capping machine applies heat-shrinkable liners to the neck of the bottle, creating a hermetic seal that prevents contamination and ensures product freshness. These machines are widely used in the packaging of food and beverage products that require high hygiene standards.
Applications and Benefits
- Food and Beverage Industry: Maintains product freshness and extends shelf life.
- 藥品: Provides tamper-evident seals for safety and compliance.
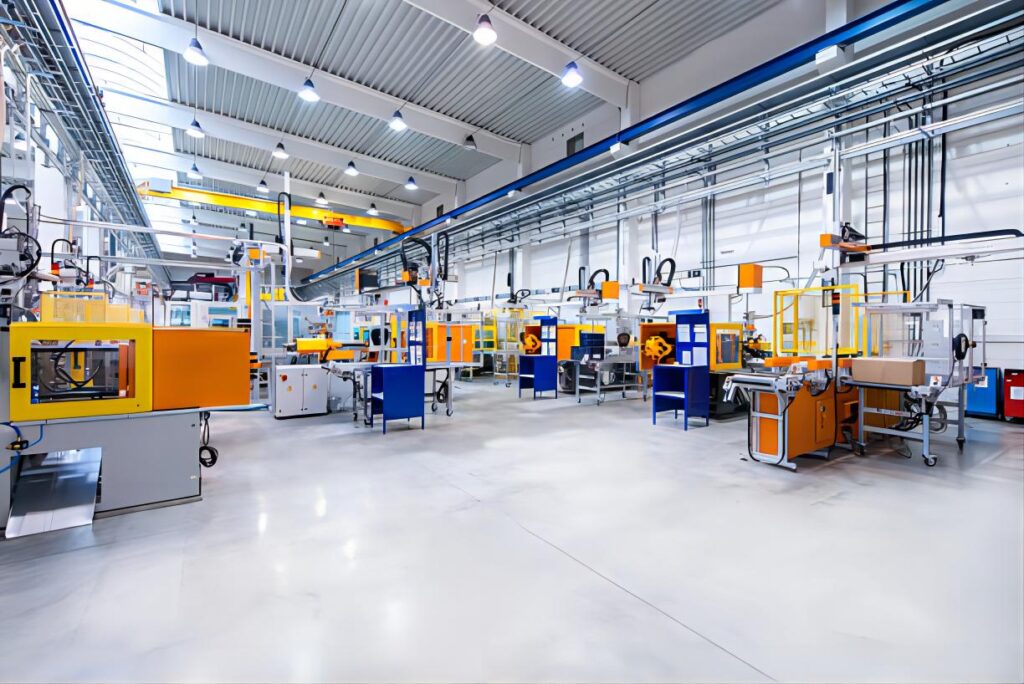
Benefits of Automatic Capping Machine
提高效率
Automatic capping machines significantly boost production efficiency by automating the capping process. This allows manufacturers to produce a higher volume of products in a shorter amount of time, meeting the demands of a growing market.
Improved Accuracy and Consistency
These machines ensure that each bottle is capped consistently and accurately, enhancing the overall quality of the product. This precision reduces waste and minimizes the risk of contamination, which is critical in industries such as food, beverage, and pharmaceuticals.
Reduced Labor Costs
By automating the capping process, manufacturers can reduce their reliance on manual labor, leading to significant cost savings. This also allows workers to focus on more complex tasks, improving overall operational efficiency.
結論
The evolution of automatic cappers has been marked by continuous innovation and technological advancement. From their early days as simple mechanical devices, they have become indispensable tools in the packaging industry, capable of handling a wide range of bottle sizes and cap types with remarkable efficiency and precision. As consumer demands and production volumes continue to rise, automatic capping machines will remain a critical component in the quest for improved manufacturing processes and product quality.